In the Food & Beverage industry, the quality of raw materials directly influences product consistency, consumer safety, and operational efficiency. Yet for many FSQA teams, procurement leads, and compliance officers, managing this critical process still means juggling clipboards, spreadsheets, and email threads. It’s inefficient, error-prone, and unsustainable in today’s fast-paced supply chains.
AuditComply’s Raw Material Auditing and Claimbacks offer a smarter way forward, one that streamlines inspections, automates financial recovery, and drives supplier accountability through one unified platform.
Digital Inspections That Start at the Source
With AuditComply’s mobile-first solution, auditors can conduct raw material inspections directly from the factory floor, even offline. Instead of scribbled notes and delayed data entry, teams capture inspection results in real-time, complete with photographic evidence of any non-conforming materials or packaging issues.
These audits are instantly synced to the cloud, ensuring that every shipment, and every issue, is recorded, traceable, and visible across the organization.
Automated Claim backs and Real-Time Calculations
One of the most impactful features is AuditComply’s ability to quantify quality issues. As soon as an audit is submitted, the platform calculates the percentage of product rejected, the financial value of the loss, and the corresponding claim amount, all using predefined formulas. This level of automation ensures accuracy, consistency, and immediate visibility into cost recovery opportunities.
Rather than relying on spreadsheets or external systems, claimbacks are managed directly within the audit workflow, enabling a faster and more structured response to supplier performance issues.
Tailored to Standards, Products, and Processes
Every supplier, ingredient, and standard is different. AuditComply’s flexible template builder allows teams to customize audit workflows based on internal SOPs or external frameworks such as FSMA, GFSI, BRCGS, and SQF. Whether auditing imported produce or local dairy, checklists can be tailored to specific regulatory or business requirements — ensuring nothing gets missed and every audit is relevant.
By embedding formula fields, grading scales, and scoring logic, the platform standardizes how performance is evaluated across regions, teams, and suppliers.
Closing the Loop with Suppliers
Audit findings are only valuable if they lead to action. AuditComply enhances supplier collaboration through a dedicated portal, allowing vendors to view audits, respond to issues, and approve or dispute claimbacks in a structured and transparent way. This level of engagement shifts the relationship from reactive to collaborative — supporting faster resolution of issues and long-term supplier development.
Internally, users can assign corrective actions, track progress, and manage communication — all within the platform, ensuring that accountability is never in question.
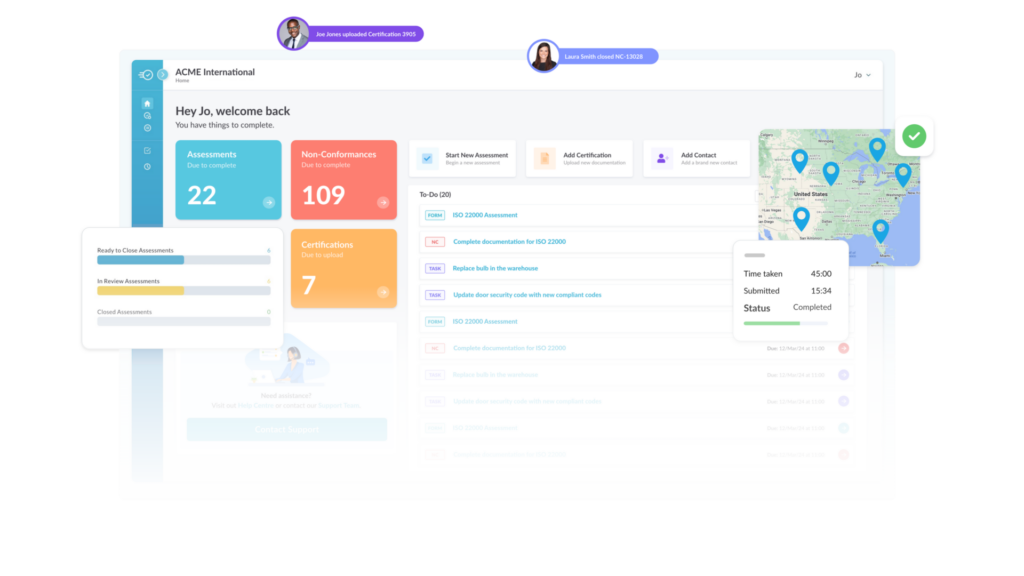
Improved Productivity, Reduced Risk, and Hard ROI
AuditComply drives measurable improvements across key operational metrics. Manual reporting time is drastically reduced, errors are minimized, and audit preparation becomes straightforward. With everything stored digitally from supplier certifications to inspection results.
Financially, the platform pays for itself quickly. Companies have recovered millions in lost revenue by consistently identifying and documenting material losses. Moreover, by analyzing audit trends and supplier scorecards, they’ve improved yields, reduced waste, and negotiated more favorable supplier agreements.
Built for the Food & Beverage Industry
Unlike generic audit software, AuditComply is purpose-built for the unique demands of the Food & Beverage sector. From raw material traceability to compliance with FSMA and GFSI standards, every element of the platform is designed to support safety, efficiency, and accountability. Features like offline functionality, photo capture, role-based dashboards, and advanced analytics ensure that teams at every level, from dock inspectors to executive leadership, have the tools and insights they need.
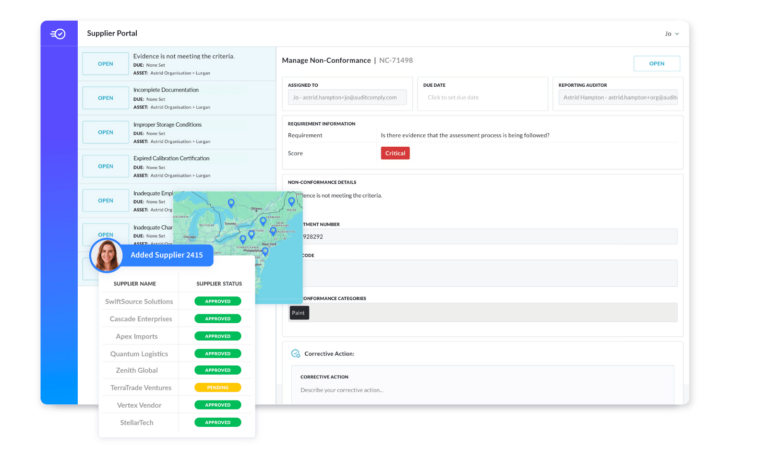
Transforming Raw Material Audits into Strategic Value
In a sector where margins are tight and standards are high, manual audit processes no longer suffice. AuditComply enables organizations to move from reactive quality control to proactive supplier management — recovering losses, improving supplier performance, and ensuring consistent compliance.
For Food & Beverage companies still relying on spreadsheets and manual workflows, AuditComply represents more than just a system upgrade, it’s a competitive advantage.
With these features, AuditComply’s supplier portal is built to tackle modern supplier management demands head-on. But how does it perform in practice? Let’s look at a real use case from a giant in the Food & Beverage distribution industry: Sysco.
Case Study: Sysco Specialty Meat & Seafood Group Supplier Portal Transformation
As the world’s largest broadline foodservice distributor, Sysco needed a streamlined way to manage food safety and supplier relationships across diverse operations. They chose AuditComply for enterprise-wide FSQA and Supplier Management, rolling it out across 25 facilities in their Specialty Meat Group (SSMG). The impact was immediate:
- Fourfold Increase in Audits: By automating manual tasks and centralizing data, Sysco could conduct more audits without adding headcount.
- Simplified Claimbacks: Raw material discrepancies—such as weight or quality shortfalls—are now logged, tracked, and resolved within the portal. Both Sysco and suppliers see claim statuses in real time, driving transparent collaboration.
- Fast Issue Resolution: Quality issues flagged in one plant trigger immediate notifications to suppliers, who must upload corrective actions in the same workflow. AuditComply eliminates ad-hoc emails and missing documents, creating a clear digital trail.
Sysco credits the platform with improved yield, better compliance, and a single source of truth for audits. Having every quality or compliance record in one portal also makes inspections a breeze—no more frantic document searches.
Embracing a Modern Supplier Solution
For companies in Manufacturing and Food & Beverage distribution, upgrading to a modern supplier portal is no longer optional. AuditComply offers a secure, collaborative space for real-time data sharing, automated workflows, and integrated compliance. It replaces manual processes and email chaos with transparency and accountability.
Rather than reacting to supplier issues after they cause disruption, a well-structured portal lets you catch red flags early, maintain continuous compliance, and build a more resilient supply chain. In a world where recalls and regulatory scrutiny are escalating, embracing a digital solution can be the difference between staying ahead of the curve—or scrambling to catch up.
About AuditComply
AuditComply is a leading enterprise technology platform designed to mitigate risk, drive compliance, and enhance quality assurance and supplier management for highly regulated industries—all within a single, connected solution. By streamlining operations, delivering deep insights, and accelerating digital transformation, AuditComply empowers organizations to improve efficiency, strengthen resilience, and ensure compliance with confidence.
If you’re facing similar challenges and want to learn more about how AuditComply can transform your Risk, Quality, Compliance, and Supplier operations, reach out to us at: info@auditcomply.com, https://www.auditcomply.com/.