Food & Beverage and Manufacturing live or die by their supply chain. For Supply Chain professionals daily life can be a never-ending juggle of compliance checks quality control issues, document chasing, and back-and-forth emails. In an age of global sourcing and remote work, these traditional supplier management methods are straining under the pressure. The good news? A modern solution is at hand: digital supplier portals designed for real-time collaboration. In this post, we’ll explore current challenges in supplier management and how a dedicated supplier portal – like AuditComply’s – can transform the way you work with vendors, with a spotlight on how Sysco achieved success.
The Challenges of Supplier Management Today
Supplier management isn’t getting any easier. Professionals responsible for supplier quality and compliance are up against a host of challenges:
- Keeping Up with Compliance: Ensuring every supplier meets regulatory standards and internal quality requirements is a tall order. Whether it’s a manufacturing standard like ISO/IATF or food safety regulations like FSMA and HACCP, there’s a constant need to collect and update certifications, audit results, and compliance documents. Many teams still rely on emails and spreadsheets for this, which can quickly become unmanageable. In fact, over 65% of procurement leaders report limited visibility into supplier performance due to fragmented, legacy systems. Without real-time oversight, issues like lapsed certifications or missed inspections can slip through the cracks, putting compliance (and your brand’s reputation) at risk.
- Quality Control Across the Supply Chain: “You’re only as good as your weakest supplier” might be a cliché, but it’s true. A single component failure or ingredient quality issue can disrupt production or spark a recall. Supplier Quality Analysts often scramble to track down the root cause of defects and coordinate corrective actions with suppliers. This process is cumbersome when communication is siloed. Important conversations get lost in email threads, and critical data might reside in one too many Excel sheets. Traditional systems leave these conversations fragmented across emails and calls, leading to information gaps and inefficiencies. The result? Slow response to quality problems and recurring issues that never get fully resolved.
- Document Exchange & Vendor Communication: From certificates to ingredient specifications, companies exchange a ton of documents with their suppliers. Chasing down a missing allergen statement or an updated ISO certificate via email is not only tedious – it’s prone to error. Version control becomes a nightmare (Was that April’s version of the SOP or May’s?). With documents scattered across inboxes or shared drives, teams waste time searching and verifying information instead of acting on it. These manual processes and data silos increase the risk of errors and eat up valuable time – procurement professionals spend up to 31% of their time on redundant manual tasks by some estimates. That’s nearly a third of your day lost to admin work that doesn’t add value.
- Lack of Collaboration & Visibility: Perhaps the biggest overarching challenge is the lack of a single source of truth. When supplier information is spread across different systems (or in someone’s personal email folders), collaboration suffers. Supplier managers can’t easily share performance data with operational teams; suppliers can’t see the status of their own compliance submissions without emailing someone for an update. This indirect, ad-hoc communication erodes trust and slows everything down. It’s telling that Deloitte found a majority of organizations still have limited visibility into what their suppliers are doing. Without visibility, you’re always reacting to the last crisis instead of preventing the next one.
These pain points are amplified in manufacturing and F&B distribution, where supply chains are complex and stakes are high. It’s no surprise that forward-thinking teams are looking for better ways to work with suppliers. Enter the digital supplier portal.
Digital Supplier Portals: A New Era of Supplier Collaboration
Imagine if working with suppliers was as easy as logging into a single platform that both you and the supplier can use. That’s the idea behind modern supplier portals. A supplier portal is a secure online platform that serves as a central hub for all interactions between a company and its suppliers. Instead of phone tag and endless email chains, both parties collaborate through one system – sharing data, documents, and updates in real time.
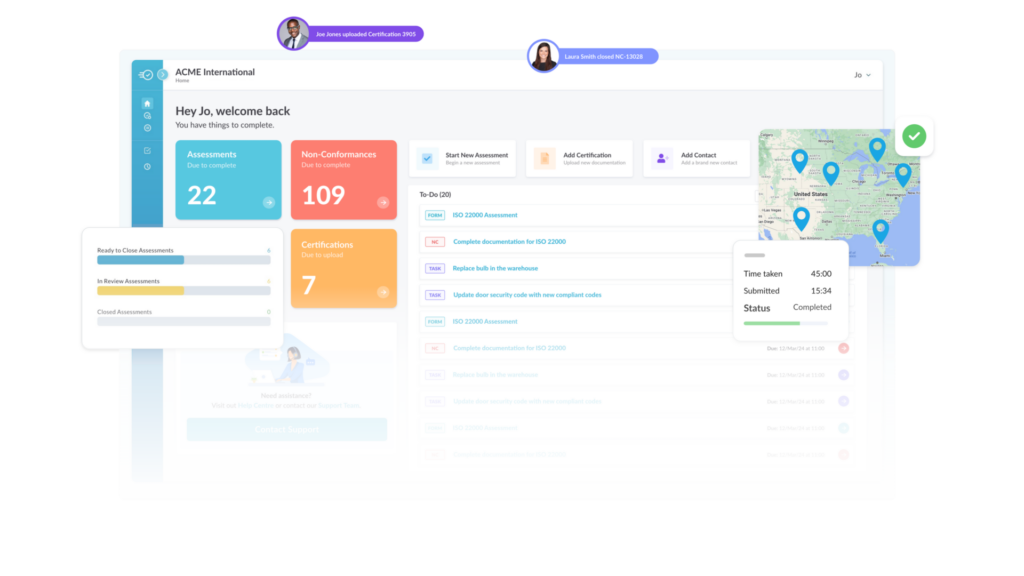
So how exactly can a digital supplier portal solve the challenges we outlined?
- One-Stop, Remote Access: A portal gives your suppliers a direct gateway into your system – and gives your team access to supplier info 24/7 from anywhere. Whether you’re on the plant floor or working from home, you can log in to see the latest status of supplier tasks or compliance documents. Suppliers, in turn, can self-service many requests (updating their certifications or responding to an audit finding) without the need for constant emails. This always-available, remote-friendly access became a lifesaver during recent years when travel was restricted and remote audits became the norm. Modern portals are designed to support this kind of distributed, anytime collaboration. In short, geography is no longer a barrier to managing supplier quality.
- Live Data & Real-Time Insights: Unlike static spreadsheets that go out of date the moment you hit “save,” a digital portal runs on live data. Supplier submitted a new quality inspection result? You can see it immediately. Product rejection trending up this week? It will reflect on the dashboard right away. Supplier portals provide a real-time 360° view of all supplier information and activity, enabling integrated risk and performance management. This live pipeline of data means you’re always working with the latest information. The benefit is twofold: your team can respond faster to issues and proactively monitor trends (so you catch that dip in quality or on-time delivery before it becomes a major problem).
- Streamlined Communication & Workflows: A good supplier portal doesn’t just store data; it facilitates action. Think of it as a collaborative workspace for you and your suppliers. Instead of discussions being buried in email, they’re tied to the actual items you’re discussing (a specific audit non-conformance or a document request). This context-rich communication is searchable and tracked. For example, if a new regulatory compliance requirement rolls out, you can coordinate the campaign through the portal: send the requirement to all suppliers, have them acknowledge and upload any needed proof, and track progress in one place. No more managing scattered email threads for a single initiative. By integrating communications into the workflow, nothing falls through the cracks and everyone stays accountable.
- Integration with Your Toolbox (e.g. PowerBI): Supplier portals don’t have to exist in a vacuum. The data they collect can feed into your broader analytics and reporting tools. Modern platforms often come with APIs or connectors to integrate with ERP systems, quality management systems, and business intelligence tools. For instance, AuditComply’s portal can seamlessly connect with enterprise software and even export data to analytics solutions like Microsoft Power BI and Tableau. This means you can mash up supplier performance data with other business metrics to get deeper insights. Want to correlate supplier defect rates with production downtime, or visualize supplier risk scores on a PowerBI dashboard? A connected portal makes that possible. Integration capabilities ensure the supplier portal enhances your existing processes rather than operates as a standalone island of data.
In essence, a digital supplier portal addresses the root causes of supplier management headaches: it breaks down data silos, automates routine tasks, and creates a shared space for collaboration. Instead of each supplier interaction being a one-off transaction, the portal fosters an ongoing partnership – with transparency on both sides. Now let’s look at how these concepts come to life with AuditComply’s solution.
Inside AuditComply’s Supplier Portal: Key Features for Modern Collaboration
AuditComply is one platform that has taken the supplier portal concept and supercharged it for real-world needs. Designed for heavily regulated industries, it delivers features that directly tackle the challenges we’ve discussed. Here’s a closer look at how AuditComply’s supplier portal makes life easier for supplier management professionals:
- Secure, Password-Free Login: Forget about juggling dozens of supplier user accounts and resetting forgotten passwords. AuditComply uses a tokenized login system – suppliers can log in via a secure email link, no permanent password required. This email-based login is not only convenient (suppliers are more likely to actually use the portal if access is easy), but it’s also safer. There are no static passwords that could be shared or stolen; each login is verified through a time-sensitive token. The result is frictionless yet secure access for your suppliers, encouraging portal adoption and frequent use.
- Easy Document Requests & Sharing: Say goodbye to chasing documents over email. With AuditComply, you can request documents (e.g. new ISO certificates, updated insurance policies, safety data sheets) directly through the portal. Suppliers get notified of what’s needed and can upload the files in a few clicks. Everything is stored in one centralized document library tied to the supplier’s profile. This means at any given time, you can check a supplier’s page and see all their submitted certificates, policies, audit reports, etc. – no detective work is required. The portal even supports automated tracking and reminders for expiring documents. For example, if a supplier’s food safety certificate is due to expire next month, the system will flag it and can automatically remind the supplier to upload a renewal. By enabling suppliers to log in and share documents (and provide evidence for compliance) in one place, AuditComply ensures seamless communication and up-to-date documentation.
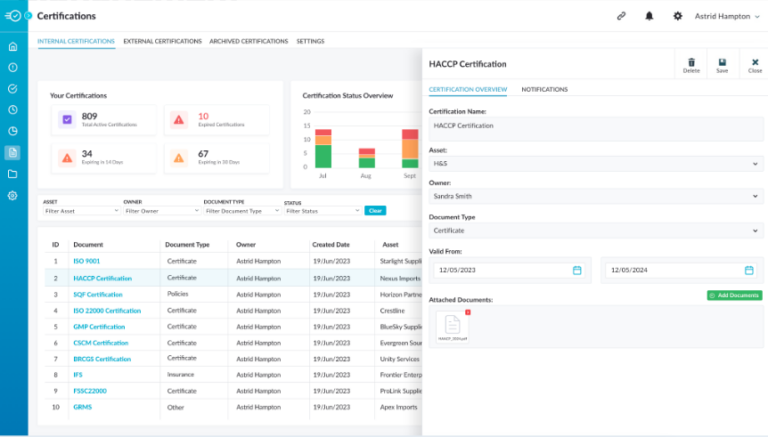
- Shared Tasks & Workflow Management: Collaboration in AuditComply’s portal goes far beyond file sharing. The platform provides a full workflow management system where you and your suppliers can work together on tasks, issues, and audits. You can assign a task to a supplier (for instance, “Correct the labeling issue on Product X and upload a photo of the fix”) and set a due date. The supplier will be notified of the pending task and deadline, and it will appear on their portal dashboard until they complete it. Both sides can track the status in real-time.
AuditComply also supports issuing audit findings or non-conformance reports to suppliers through the portal. Suppliers can log in to view the issue, attach their corrective action evidence, and mark it resolved – all within the same thread. This “assign, action, and communicate” approach keeps everyone on the same page. No more lost emails or excuses; every request and response is documented. The portal essentially creates a living to-do list shared between you and each supplier, with automated workflows to streamline approvals and follow-ups. It’s a far cry from the old days of chaotic email chains and forgotten promises. - Real-Time Performance Tracking & Scoring: Remember the days of compiling monthly supplier scorecards in Excel? AuditComply eliminates that manual labor. As suppliers interact with the portal – completing self-assessments, submitting quality data, undergoing audits – the platform is automatically aggregating that information into performance metrics. AuditComply’s scoring engine can grade suppliers based on gathered data, producing risk scores or quality ratings that update in real time.
You get a live supplier dashboard showing key KPIs: audit scores, product claims ($), non-conformance rate, etc., tailored to what matters for your business. This real-time scoring isn’t just for your eyes; you can choose to share relevant performance feedback with suppliers too. Many AuditComply users leverage this to drive improvement – for example, showing a supplier their trend in defect rate versus the target. Because the data is updated continuously, you can spot performance dips early and address them proactively. Additionally, AuditComply performs instant compliance checks on things like certifications. If a required cert or document is missing, you’ll see that flagged immediately on the supplier’s profile. In short, the portal provides an always-up-to-date report card for each supplier, without the need for tedious data crunching on your part.
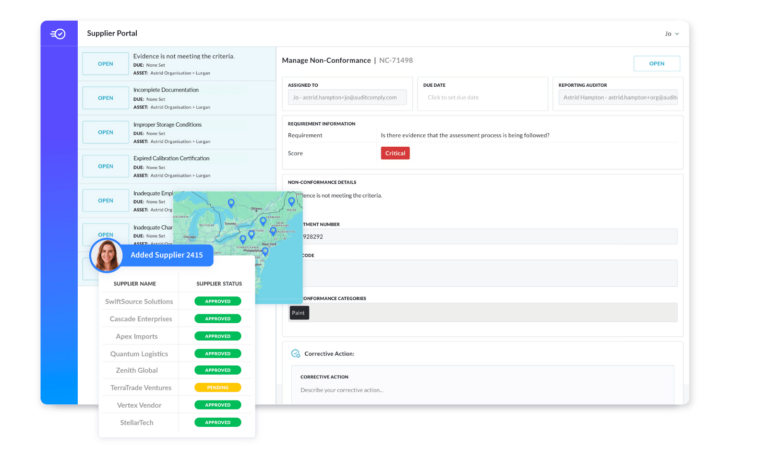
- Remote Engagement Capabilities: In today’s world, not every audit or meeting can be on-site. AuditComply’s platform is built with remote engagement in mind. Suppliers and auditors can perform many activities remotely via the portal – from digital audits (with suppliers uploading photos/videos as evidence) to our mobile app. This proved critical for companies adapting to travel restrictions; having a remote-ready supplier management model ensures that quality and compliance oversight continues uninterrupted. AuditComply supports a hybrid approach – you can engage suppliers in person when needed and handle a lot of the routine follow-ups and data collection remotely through the portal. It brings your suppliers “on site” digitally, whenever you need them.
- Integration & Analytics (PowerBI-Ready): AuditComply knows it’s part of a larger tech ecosystem for most organizations. Thus, it offers robust integration options to ensure data flows where it needs to. Through a well-documented REST API and out-of-the-box connectors, AuditComply can sync with popular ERP systems (SAP, Oracle, etc.), quality management software, and BI tools. Notably, it supports direct integration with Microsoft Power BI and other analytics platforms.
This means you can push supplier performance data from AuditComply into Power BI to create custom dashboards or combine it with other data sources. For example, one could integrate AuditComply’s supplier risk scores with internal cost data in Power BI to see if lower-performing suppliers are also driving higher warranty costs. The integration is secure and real-time, thanks to webhooks and automated data exchange features. For a supplier manager, this capability is a huge win – you get all the benefits of AuditComply’s portal and you can leverage your existing analytics investment to slice and dice the data any way you want. It’s about making supplier data not only easier to capture, but easier to use for strategic decisions.
With these features, AuditComply’s supplier portal is built to tackle modern supplier management demands head-on. But how does it perform in practice? Let’s look at a real use case from a giant in the Food & Beverage distribution industry: Sysco.
Case Study: Sysco Specialty Meat & Seafood Group Supplier Portal Transformation
As the world’s largest broadline foodservice distributor, Sysco needed a streamlined way to manage food safety and supplier relationships across diverse operations. They chose AuditComply for enterprise-wide FSQA and Supplier Management, rolling it out across 25 facilities in their Specialty Meat Group (SSMG). The impact was immediate:
- Fourfold Increase in Audits: By automating manual tasks and centralizing data, Sysco could conduct more audits without adding headcount.
- Simplified Claimbacks: Raw material discrepancies—such as weight or quality shortfalls—are now logged, tracked, and resolved within the portal. Both Sysco and suppliers see claim statuses in real time, driving transparent collaboration.
- Fast Issue Resolution: Quality issues flagged in one plant trigger immediate notifications to suppliers, who must upload corrective actions in the same workflow. AuditComply eliminates ad-hoc emails and missing documents, creating a clear digital trail.
Sysco credits the platform with improved yield, better compliance, and a single source of truth for audits. Having every quality or compliance record in one portal also makes inspections a breeze—no more frantic document searches.
Embracing a Modern Supplier Solution
For companies in Manufacturing and Food & Beverage distribution, upgrading to a modern supplier portal is no longer optional. AuditComply offers a secure, collaborative space for real-time data sharing, automated workflows, and integrated compliance. It replaces manual processes and email chaos with transparency and accountability.
Rather than reacting to supplier issues after they cause disruption, a well-structured portal lets you catch red flags early, maintain continuous compliance, and build a more resilient supply chain. In a world where recalls and regulatory scrutiny are escalating, embracing a digital solution can be the difference between staying ahead of the curve—or scrambling to catch up.
About AuditComply
AuditComply is a leading enterprise technology platform designed to mitigate risk, drive compliance, and enhance quality assurance and supplier management for highly regulated industries—all within a single, connected solution. By streamlining operations, delivering deep insights, and accelerating digital transformation, AuditComply empowers organizations to improve efficiency, strengthen resilience, and ensure compliance with confidence.
If you’re facing similar challenges and want to learn more about how AuditComply can transform your Risk, Quality, Compliance, and Supplier operations, reach out to us at: info@auditcomply.com, https://www.auditcomply.com/.