BRCGS Issue 9: 4 Steps to Digitizing Your Food Safety & Quality System
Richard Wilson February 13, 2023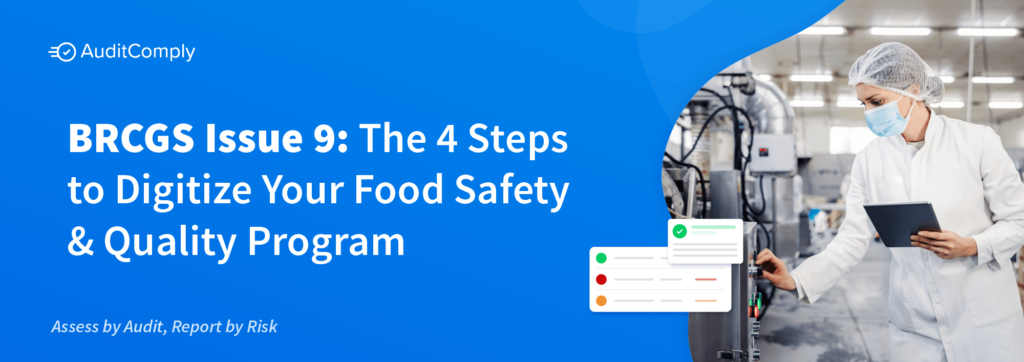
BRC Global Standards is a leading brand and consumer protection organization, providing assurance to consumers and customers across the food supply chain through the creation and implementation of rigorous and globally recognized food safety, packaging, and product standards.
BRCGS Issue 9 is the latest version of its Global Standard for Food Safety, which provides a framework for companies in the food and packaging industries to ensure the safety and quality of their products. BRCGS Issue 9 represents a major update to the previous version, with a stronger focus on risk-based thinking, continuous improvement, and a more comprehensive approach to supplier approval and management. The standard has been updated to reflect the latest food safety legislation and best practices, as well as to provide greater clarity and consistency in the interpretation and application of its requirements.
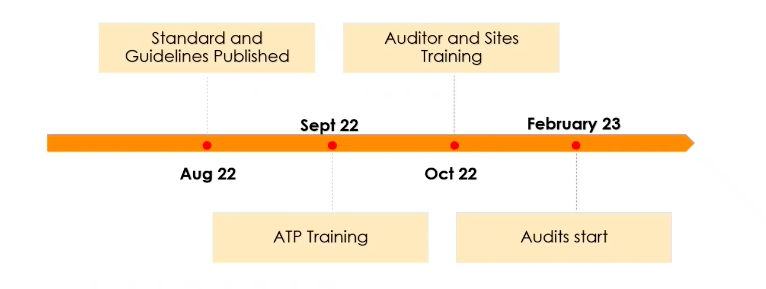
Implementing a digital food safety system for BRCGS Issue 9 is crucial in ensuring that food products are safe for consumption and meet the required standards. By adopting a digital food safety system, organizations can streamline their processes and make it easier to comply with the requirements set out in Issue 9. This can help to reduce the risk of food safety incidents and ensure that products are consistently manufactured to high standards.
Additionally, a digital system can provide real-time monitoring and reporting, enabling organizations to quickly identify and address any potential food safety issues. By investing in a digital food safety system, organizations can demonstrate their commitment to food safety and quality, which is essential in building customer trust and confidence in their products. Below we outline the 4 necessary steps your food organization can take to ensure a successful digital Food Safety & Quality Assurance (FSQA) system implementation.
Step One: Assess Your Current FSQMS
Start by evaluating your current processes and systems to identify areas where digitization can improve efficiency and accuracy. Consider the specific needs of your organization, such as regulatory requirements, product types, and supply chain management.
Familiarize yourself with the changes in the updated standard. You can get a breakdown of the changes in our guide to the changes document here, or you can purchase a copy of the updated standard directly from the BRCGS website. This guide can be used to introduce the BRCGS Food Safety to your management team and outline the requirements when considering a new FSQMS.
Step Two: Selecting The Right Technology
Consider the different types of technology available and select the one that best suits your needs. This could include software specifically designed for food safety and quality management, cloud-based systems, or mobile apps. Ensure that the technology you choose is easy to use, secure, and reliable. When selecting a FSQMS, here are some key factors to consider:
- Compliance with regulations: Ensure that the platform meets the regulatory requirements for your industry, such as BRCGS Issue 9, FDA Food Safety Modernization Act (FSMA), and Global Food Safety Initiative (GFSI) standards.
- Ease of use: Choose a platform that is user-friendly, intuitive, and accessible to all members of your team.
- Data security: Ensure that the platform has robust security measures in place to protect sensitive information, such as personal data and food safety records.
- Real-time tracking and reporting: Choose a platform that provides real-time monitoring and reporting capabilities, enabling you to quickly identify and address food safety issues.
- Customization: Look for a platform that can be customized to meet the specific needs of your organization, such as product types, supply chain management, and process flows. Integration with existing systems: Ensure that the platform can integrate with your existing systems, such as accounting software, enterprise resource planning (ERP) systems, and laboratory information management systems (LIMS).
- Support and maintenance: Consider the level of support and maintenance provided by the vendor, such as training, technical support, and software updates. By considering these factors, you can select a food safety and quality management platform that meets your specific needs and helps you to ensure the safety and quality of your food products.
Step Three: Culture & Leadership Commitment
Creating a food safety culture through digital transformation is important because it helps to embed a strong commitment to food safety and quality throughout an organization. Digital transformation can provide a comprehensive and integrated approach to food safety and quality management, enabling organizations to:
- Streamline processes: Digital systems can automate routine tasks and simplify complex processes, reducing the risk of human error and improving efficiency.
- Enhance collaboration: Digital systems can facilitate communication and collaboration between different departments and stakeholders, improving the accuracy and speed of decision-making.
- Ensure accountability: Digital systems can provide a clear audit trail and enable organizations to track and report on food safety and quality performance in real-time, making it easier to identify and address issues.
- Foster a culture of continuous improvement: Digital systems can provide valuable insights into food safety and quality performance, enabling organizations to identify areas for improvement and continuously enhance their systems.
- Build customer trust and confidence: By demonstrating a commitment to food safety and quality through the use of digital systems, organizations can build trust and confidence with customers and stakeholders.
The support and endorsement of senior leadership is critical for the success of new technology implementation within an organization. When senior leaders are invested and committed to a technology, it sends a strong message to the rest of the organization, demonstrating the importance and value of the technology. This can increase the adoption rate and usage of the technology, leading to improved business processes and outcomes. A Senior Management Implementation checklist has been published by BRCGS and can be found in their handbook here. The checklist establishes your Food Safety Management System fundamentals including Food Safety Policies and Objectives.
The checklist guides Senior Management in planning the establishment of the FSQMS; providing adequate support to establish the FSQMS ;ensuring there is adequate infrastructure and work environment and in allocating responsibility and authority.
Once you have chosen the right technology, implement it throughout your organization, and train your employees on how to use it to help embed it effectively within your organization. Ensure that everyone understands the importance of using the system and how it will improve food safety and quality.
Step Four: Monitor & Maintain
Regularly monitor the system to ensure it is working effectively, and make any necessary updates or improvements. Continuously evaluate the system to identify any potential weaknesses and address them before they become significant issues. Keeping the system up-to-date and in good working order is essential for ensuring the safety and quality of your food products.
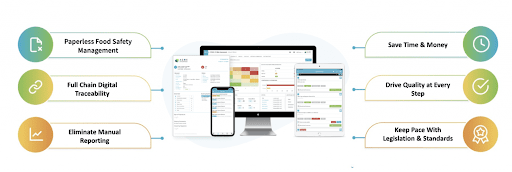
Overall, BRCGS Issue 9 represents a significant step forward in the assurance of food safety and quality for companies operating in the food and packaging industries. By adopting and implementing the standard, companies can demonstrate their commitment to food safety and provide their customers and consumers with confidence in the safety and quality of their products.
To find out how AuditComply can be your secret weapon in achieving AA+ grades across all your sites. Join our upcoming webinar on BRCGS Issue 9: Digitizing Your Food Safety & Quality Program or request a demo and see for yourself.